Review of the Roland LG-640 (2023-Nov) Do NOT buy!
As little info is available online regarding the Roland LG-640 (LG-540 & LG300) I decided to write a little review of my experience with the new Roland LG-640 during the last 4 to 5 weeks.
TL;DR. Do NOT buy. Reasoning.
- Excess amount of ink wastage in drainage bottle. Over € 9.200 euro (> US$ 10.000) a year.
- The amount of ink you put on the media cannot be controlled/changed.
- Speed is significantly below the 12 year old XR-640.
- No deep CMYK black, it is simply a dark brown!
- The horrible smell.
Our background.
We have been printing with Roland printer for about 25 to 30 years (at the moment a XR-640 and a VS-540 with eco-sol max 3 L ). And we have also been using Roland cutters, up to and including the Roland CM-500. After which we mainly started using Summa’s Tangential cutters.
If you have any questions. Let me know.
- Running cost are absurd high of the Roland LG-640.
The amount of ink the printer throws away in the drain-bottle is simply unacceptable.
We printed for 7 days straight, after receiving the printer, to get a good feel of the machine. And boy was it disappointing. According to Roland 16 meter a day (52 feet) was printed during this time. Of those 16 meters, I would say about 5 to 10 m2 was completely covered with ink. After these 7 days, about 40 printing hours I would say, the printer had dumped more-or-less exactly 1,4 litres (1400ml) of ink into the drain bottle (200ml a day). At € 130 euro for a 750ml cassette this equals to about € 242 euro (1,4*130/0,750) (1 Euro is 1,09 US Dollar).
The printer also dumps about 30 ml a day in the drain bottle, if you do not use the machine. Based on 250 working days this will cost you 250*200ml + 115*30ml = 53,45 L a year.
Our existing machines do not even dump 6L into their drain bottles combined, a year.
This will cost you 53,45L * €130/0,750ml = € 9.264 every year if you use the machine for about 5 hours a day (production speed of this machine is about 3 meter an hour effectively, more on this later).
The excessive ink consumption completely defeats the purpose of switching from eco-sol to UV!!!
According to Roland themselves the “running costs” or the maintenance consumption per day of the Roland LG-640 is 5.7 to 7.6 times higher compared to the Roland MG-640 the previous generation. See the image below. /edit added on 22-dec-’23
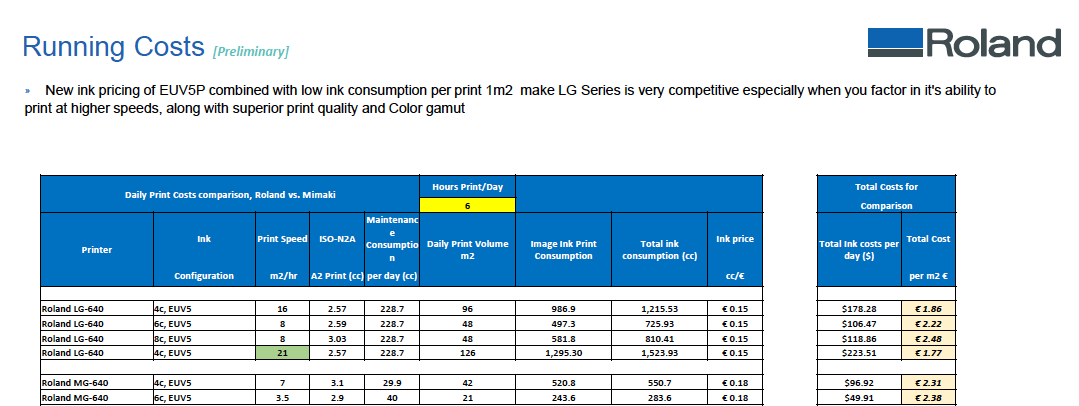
Roland LG 640 high running (ink) costs compared to Roland MG-640 and other printers
- No print profile control.
The printer comes with 6 generic print profiles. Of which 5 are basically the same, with little to no difference. Whereas with eco-sol printers you can very the amount of ink you put on the media to a very large degree, this is simply not possible for the Roland LG-640. It will put very little ink on the media (and an excessive amount in the drain bottle). Thus, making the machine (almost) completely useless for printing on transparent/translucent media.
In addition, you will be unable to match (extremely limited in matching) a eco-sol gloss print with a UV mat print (on transparent/translucent media).
The sixed print profile is backlit which a basically just overprint. This slows the machine down to under 2 meters a hour.
- Production speed of the Roland LG-640 printer.
When in quality mode “General Sign Production” 900x720dpi the print speed of the LG-640 is more or less comparable to the XR-640 print speed of 720x720dpi. About 6000x1300mm an hour.
However, the production speed of the printer is way below 6 meters a hour. Because of the following two reasons, the production speed of the Roland LG-640 is significant below expectations.
One. Due to WAY too many maintenance, cleaning and ink cycles. The ink usage of the machine is simply unacceptable (nov-2023). For small print jobs, the machine needs an excessive amount of time doing maintenance, cleaning and ink cycles compared to doing very little printing. Especially if you do a couple of small prints with white on top or under a colour layer. The machines will spend more time doing ink/maintenance/cleaning cycles than printing!
It will continuously do cycles before, during!?! and after prints.
Every 6 hours the printer runs a maintenance cycle, when off. If you turn the printer on, just 5 minutes after it has run such a cycle, it will again run a maintenance cycle!?! Crazy! I hope they can/will fix this in a firmware update.
It will be about 8 minutes before you can use the printer when you turn it on.
Two. Too little ink on the media. Thus needing to use overprint, way more compared to a eco-sol printer, to get an acceptable end result. Overprint reduces the speed of the print speed to less than 2 meters an hour.
Overall production speed is significantly lower compared to our Roland XR-640. Disappointing to say the least, as the XR-640 was introduced by Roland over 11 years ago in 2012 in the EU.
- Colours. No black for you!
Printing CMYK black in not a deep black compared to the eco-sol CMYK black. It is almost a dark brown. An eco-sol CMYK black will fit almost perfectly besides a black coloured vinyl but black printed on the Roland LG-640 sticks out as not being black!
Solution? None! Switching to a RGB black gives better blacks (a darker black) on the LG-640, but this is not a solution. The printer simply uses too little black ink to make a nice black on white vinyl. Using a different print mode/quality does not change this. Only using overprint solves this, but this is unacceptable.
Conclusion. So printing a nice CMYK black with the Roland LG-640 is not really possible, at this moment.
The orange and red cassettes create great red colours, especially compared to the poor red colours of the eco-sol max 3 ink.
- The smell!
The machine sure smells. Much much more and worse compared to an eco-solvent machine. I would strongly advise putting it in a separate room.
Banding.
Machine was installed by a Roland dealer. It uses more or less the same calibration as the eco-sol machines. Banding was, and is still, present from the beginning in most prints, especially on transparent/translucent media.
Print Quality.
Very nice mat finished end result, very nice colours, just beautiful.
3 layer prints (colour – white – colour).
Nice for small stickers, but not really useable for cut-to-shape signage. Our application tape does not stick to this type of 3-layer print work. We use R-tape high tack 4075. You will have to laminate the film/designs first for the application tape will stick to it (which I would not advise given the very ruff/bumpy surface of a 2 and 3 layer print).
It is, at the moment, not possible to print 3 layers in one go. You print, return printer to origin when finished and you print again on top. Colour – white in the first pass and subsequently colour in the second pass.
Regressions.
- Cut force cannot be changed during print or cut. WTF??? This is immensely stupid.
- It is not present on the main page of the machine. It should be present on the main menu and you should be able to change the cut force at any one time.
- Cut sheet now requires 2 button presses instead of 1. Like many other actions now require way too many navigations/button presses. Again slowing everything down.
Display.
Does not show force of the blade or have an indicator for the level of the cleaning cassette. You will be pressing a lot more buttons, compared to a XR.
Pickup unit.
You now have 2 different ways to roll the material onto the cardboard tube/core. VERY handy. The new method keeps the material coming out of the printer lose, as it does not put tension on it. VERY handy.
Energy consumption of the Roland LG-640 printer.
Below expectations, in a good way. Specs say 800 watts. But real world usage of energy is much lower. 180 to 220 watts when printing, around 75 to 80 watts when not printing and about 45 watts with secondary power off.
Thus, energy consumption during printing is much lower compared to the XR-640 with the additional front heater. With secondary power off, the energy consumption of both printers is about the same.
The BOFA fume extractor consumes about an additional 80-110 watts when in use. I measured around 108 watts on average during the day.
Cutting.
Unlike solvent prints the printed part with UV are thicker compared to the unprinted parts. Whereas with eco-sol you use the same cut force for printed and unprinted part. You will need more force for the printed parts compared to the unprinted parts. Especially for 2 and 3 layer prints. Thus, media with thin backing can/will give problems.
Other issues of the Roland LG-640 printer.
- The lip on the left of the metal UV guard on the back bends VERY easily, thus continuously dropping the guard/lit on your “fingers.” Very annoying.
- Heavy roll carriers in the middle of the machines, crease the vinyl, so (re)move them!
- Move them to the sides and flip them over.
- Media clamps accumulate a lot of adhesive at the bottom. We “never” had to clean the media clamps of the XR-640 in 7 years. We needed to clean the media clamps of the LG-640 within a week (a couple of days). Similarly they are collecting UV ink on top.
- Do not use the media clamps on vinyl (cheap Chinese stuff) that has shrunk on the backing exposing a little adhesive. Media will stick to the clamps and printing and/or cutting will cause media errors.
- It looks like the new media-clamps scrape more onto/into the material and thus accumulate adhesive on their bottom.
- They are black and very hard to see. Roland please make them Roland blue, so they are easier to see.
- Move them to the side when loading media, otherwise they will always be in the way.
- The printer is very dark and closed (they do not want the UV light to escape/reflect. As a result make sure you have a flashlight to easily see inside (when removing/cleaning your media clamps, etc.).
- The digital display nicely shows the ink level of the 8 ink cartridges/cassettes. However, is does not show the level of the 9th cassette, the cleaning cassette.
- You will definitely forget to buy a cleaning cassette in time. I expect the printer will not work when this cassette is empty?
- Printer does not want to print when the drain-bottle is half full.
- This is up the operator to decide, not the printer, especially when the drain bottle is half!!! full.
- When you are in the menu you have to manually navigate out of the menu to the main screen or the printer will not print. WTF???
- The ink stays in the holes of perforated films (if the media is not UV ink “compliant” ).
Bugs.
Software (firmware machine and Versawork) is mature. Not a lot of bugs encountered.
- 1x No ink/cartridges present error, needed to turn the printer off, and printer again needed 10 minutes for maintenance before it was ready.
- 1x Network error, black screen with white lettering, needed to turn the printer off, and printer again needed 10 minutes for maintenance before it was ready.
- White not being printed, while it correctly shows in the rip (that it is present).
- Blade force was set to 50 gr, all was fine. All of a sudden the blade would not cut proper any more (not enough force). Replaced the blade. Still did not work. Increased the force to 100 gr and it cut again the same as it previously did on 50 gr of force.
Conclusion of my Roland LG-640 review.
Problems/limitations have been reported to the Roland dealer and Roland. None have been disputed.
So the printer has a (very) limited usability, only for very small specific niches. I would only recommend using this machine on mat white vinyl (ignoring the cost issue). As it produces a very nice mat print (use RGB black instead of CMYK black in your prints) (yes this will be a big pain in the butt and not really viable).
From an economic and environmental perspective this machine is completely unacceptable. Thus, should not be purchased by 99% of sign makers (in my opinion).
Questions? Let me know.
/edit 12-dec-’23
Did another test last thursday. 44m2 of print files (took about 13 hours). Versaworks said it needed 253ml (41%) of ink. After printing the drain bottle contained 370ml (59%) of ink/liquids (during a 26 hour period). 🙁 Completely unacceptable. Machine is going back to the dealer.
Today did some little prints. Again a bunch of those strange “network error” and “no ink cartridges” errors. Printer needed to power completely down to reset and become available/usable. Needed about 3 maintenance/ink cycles. Which will result in you having to wait 20 to 30 minutes before you can start printing. : ( (So second time in about 15 days of usage, during the last 6 weeks)
Small math calculation. 250 working days for 8 years, times 370ml of wasted ink/liquids it about 740L during the lifetime of the printer. 740 * (€140/750ml) = €138K
If the printer would no through away so much ink, we would be keeping the printer. But from a environmental and economic perspective this machine is unacceptable.